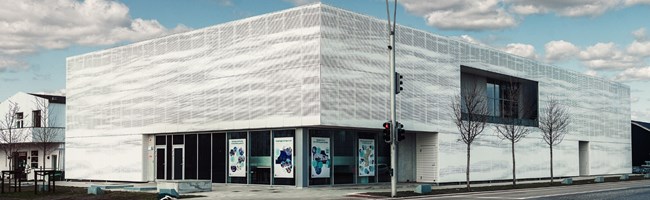
Cascade heat pump for district heating
A cascade heat pump used for the supply of district heating.
Picture by KOLLISION
Heat pump system
Affaldsvarme Aarhus, the local district heating operator, is using an electricity driven cascade heat pump for the supply of district heating to the local distribution net. The system consists of a steam compression cycle, which is recovering heat from seawater in an open evaporator. On top, a single-stage ammonia system is upgrading the heat for supply to the district heating network.
The steam compression system is a novel system and the first of its kind. Through the construction with an open evaporator, it is possible to recover heat from seawater, while avoiding challenges related to fouling and icing. The challenge for this kind of system is the compression system. Therefore, a special multi-stage axial compressor has been developed. The ammonia system is a conventional single-stage reciprocating compression system.
Figure 1: Simplified flow sheet of cascade heat pump system.
Figure 2: Steam compression system during installation (left) and single-stage ammonia system (right).
The unit has a nominal supply capacity of approximately 1 MW, and it is located in the Machine Room on Aarhus Ø, Denmark. The plan is to install up to 14 units at the same location.
Digital twin-based services
Heat pumps are considered as the key-technology for decarbonizing the Danish district heating sector, and a massive deployment is expected during the next few years. However, the experiences with the heat pump technology are somewhat limited for district heating operators, especially when it comes to first-of-its-kind equipment as the steam compression system. In this context, it will be crucial to gain as much as possible knowledge about the technology and learn how to operate it in the most optimal way as well as to find out how the system will behave in other operating conditions.
The activities in this project aim at providing a numerical model-based support for forecasting operating behavior and finding the most optimal operating conditions in a variety of operating conditions. These operating conditions might be standard operating conditions, extreme conditions, such as supply of higher forward temperatures or during a flexible operation mode to supply flexibility to the electricity market. In addition, the numerical models will enable the monitoring of fault mechanisms and create the basis for predicting alarms and breakdowns in order to take respective precautions and reduce downtime.